Why MTD
Invested in Innovation
We don’t just talk about innovation. We invest in it.
To be the best partner we can be for our customers, we invest 10% of our annual revenue to innovation. Our internal R&D projects explore what new micro molding capabilities we can create, so our customers can achieve new product breakthroughs faster and more cost-effectively. In fact, we are the first in our industry to have an R&D engineer devoted solely to these projects. This allows a continuous exploration of topics like:
- What new capabilities will emerging trends require?
- What roadblocks are OEMs running into with their breakthrough ideas?
- How can we adopt and adapt cutting-edge equipment to drive precision and efficiency?
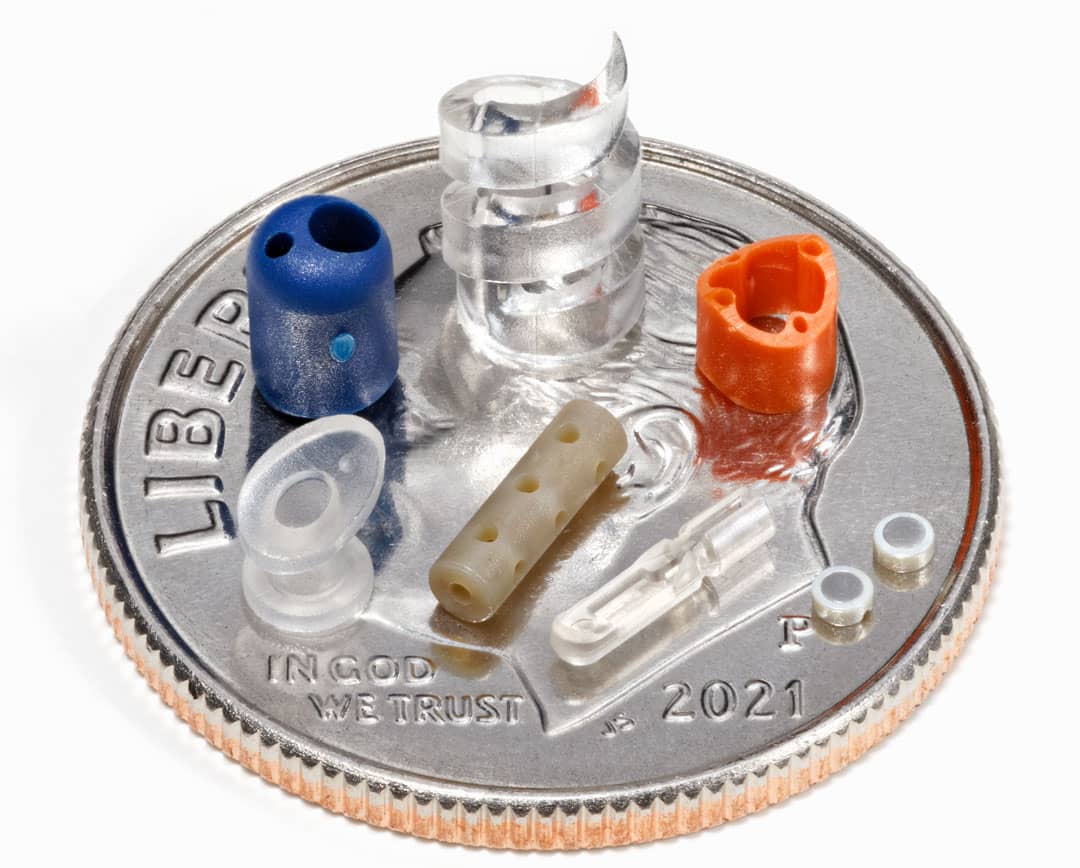
We invest a dime for every dollar.
I have had the pleasure of working with MTD for the past 5 years and have been impressed by their continued investment in new technologies. MTD is constantly adding new capabilities and it has translated into improved product quality for our micro-molded components.
Runner Optimization R&D Project
One of MTD’s internal R&D project explored minimizing runner length in bioabsorbable materials to dramatically reduce costs.
Pictured here is an example of runner optimization. On the left is the first runner iteration, and the right shows where MTD is today — an optimized runner system with 50% less material than before.
Other R&D Projects
Here are other examples of how we have turned roadblocks into building blocks:
- Bringing critical material testing processes in-house like Inherent Viscosity (IV), Gas Chromatography, and Differential Scanning Calorimetry (DSC)
- Challenging rules of injection molding and micro injection molding to build our own processing database for various polymers
- In-house 3D-printing to support custom molding automation
- Introducing multi-axis robotics to molding cells for custom packaging solutions