Why MTD
Validated Production
The goal of all MTD’s medical injection molding projects is validated production, with the intended result of the validation activities being a robust molding process. This process, when challenged by introducing variation to the critical variables, must result in products that will meet the agreed upon capabilities.
MTD’s validation strategy is based on the IQ, OQ, PQ process. To what extent this is carried out on each project will be determined by mutual agreement between the customer and MTD Micro Molding. Where we are directed by customer requirements, the customer strategy will prevail, and the validation will be carried out as per customer requirements. In any instance that there are no specific customer requirements, this MTD Micro Molding IQ, OQ, PQ process will be implemented.
In-line 6-axis robot places micromolded parts in Gel-Paks.
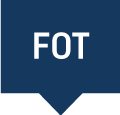
Installation Qualification (IQ), FOT
Following mold completion, IQ will occur, resulting in FOT samples. This is a basic mold test to verify the mechanical functionality of the mold and to create initial samples for the customer to evaluate, along with a brief report while establishing a baseline molding process.
Because we take the time to start with quality tooling, MTD achieves a 90% first shot rate.
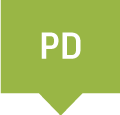
Process Development
Process development is performed to qualify a process window that produces acceptable parts. The intention of this phase is to create a robust molding process and then evaluate the corresponding capability relative to dimensional and visual criteria. Scientific Injection molding procedures are performed at this time to determine optimal process conditions. A measurement system is created and analyzed with a Gauge R&R for all the critical dimensions.
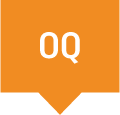
Operational Qualification (OQ)
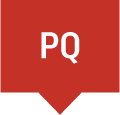
Performance Qualification (PQ)
A final report will be generated and submitted to the customer for final validation approval. This final approval will signify that the mold is approved for production.
Bioabsorbable Validation
Validating a bioabsorbable part requires more steps than a non-bioabsorbable part, but with good planning and exact execution, the timeline to get to production is far from daunting. With a collaborative approach, a micro molder should fully document and customize their validation processes for each client and project.

Production
- Lights out manufacturing (24/7)
- Integrated, automated vision capabilities
- In-line verification of part and runner
- In-line verification of presence/absence of part features
- ETDL-process condition monitoring
- SPC-process control software
- RJG-EDART instrumented cavities
- Automated part removal with custom end-of-arm tooling (EOAT)
- Separation by cavity
- Degating operations
- Custom packaging