MTD MicroSeries
The MTD MicroSeries is a collection of medical micromolding industry briefs, based on more than 5 decades of experience. We discuss a range of micromolding topics, from understanding the capabilities of micro technology to learning about the latest medical device manufacturing breakthroughs.
New
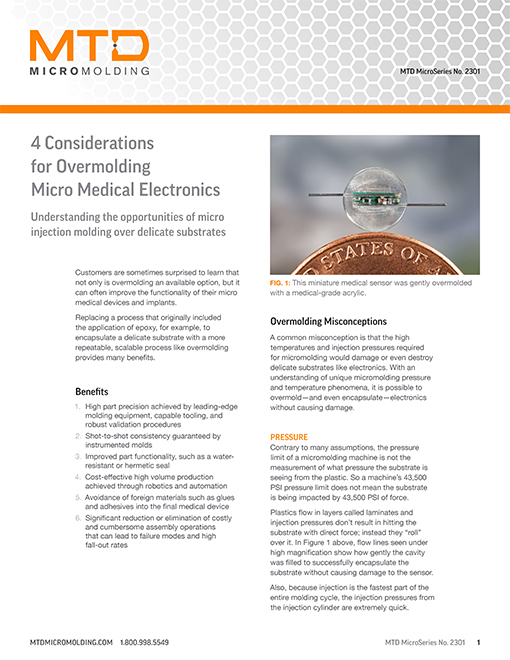
Issue 2301
4 Considerations for Overmolding Micro Medical Electronics
Understanding the opportunities of micro injection molding over delicate substrates
Medical OEMs are sometimes surprised to learn that not only is overmolding an available option, but it can often improve the functionality of their micro medical devices and implants. Learn how it is possible to overmold—and even encapsulate—electronics without causing damage.
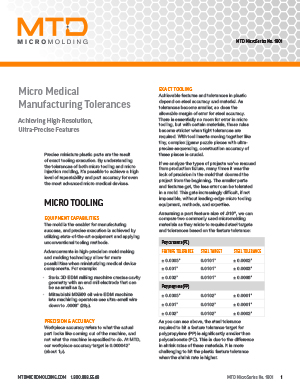
Issue 1901
Micro Medical Manufacturing Tolerances
Achieving High-Resolution, Ultra-Precise Features
Precise miniature plastic parts are the result of exact tooling execution. By understanding the tolerances of both micro tooling and micro injection molding, it’s possible to achieve a high level of repeatability and part accuracy for even the most advanced micro medical devices.
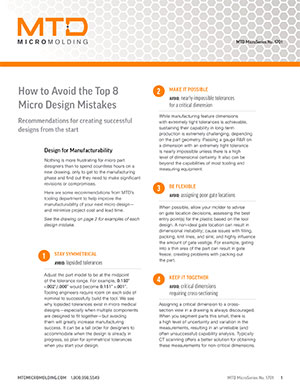
Issue 1701
How to Avoid the Top 8 Micro Design Mistakes
Recommendations for creating successful designs from the start
Nothing is more frustrating for micro part designers than to spend countless hours on a new drawing, only to get to the manufacturing phase and find out they need to make significant revisions or compromises. Learn how to improve the manufacturability of your next micro design.
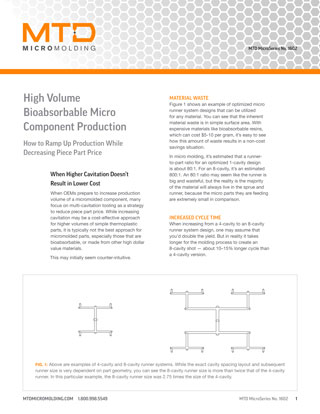
Issue 1602
High Volume Bioabsorbable Micro Component Production
How to Ramp Up Production While Decreasing Piece Part Price
When OEMs prepare to increase production volume of a micromolded component, many focus on multi-cavitation tooling as a strategy to reduce piece part price. While increasing cavitation may be a cost-effective approach for higher volumes of simple thermoplastic parts, it is typically not the best approach for micromolded parts, especially those that are bioabsorbable, or made from other high dollar value materials.
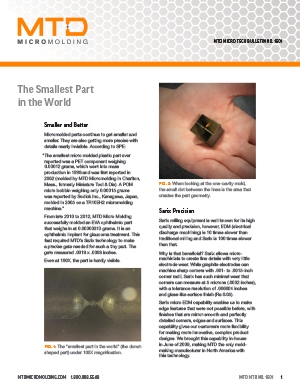
Issue 1601
The Smallest Part in the World
From late 2010 to 2012, MTD Micro Molding successfully molded an EVA ophthalmic part that weighs in at 0.00000313 grams. It is an ophthalmic implant for glaucoma treatment. This feat required MTD’s Sarix technology to make a precise gate needed for such a tiny part. The gate measured .0018 x .0008 inches.