One of the most common questions that our team hears from medical OEMs seems simple: how thin can we go?
But the answer is: it depends.
One of the main factors is material choice. Can your design use a thermoplastic material that’s better suited for ultra-thin walls, like LCP? Or does your part functionality require other material characteristics, like the rigidity of PEEK, which is much more challenging for thin-wall molding? Or does your thin wall design require multiple materials for an overmolded component?
While our team of micro molding engineers may ask you several questions before they can accurately answer just how thin your medical device’s walls can be, here are a few insights to keep in mind.
1. What are the best materials for molding extremely thin-walled medical components?
Even when you have the option to use the best materials for molding ultra-thin walls, keep in mind that the thinnest wall highly depends on your part’s geometry and aspect ratios.
Material | Thinnest wall possible* |
1. LCP | .002” |
2. Polypropylene | .002” |
3. Polyester | .004” |
4. Nylon | .004” |
*Achievable thinnest wall value highly dependent on geometry and aspect ratio.
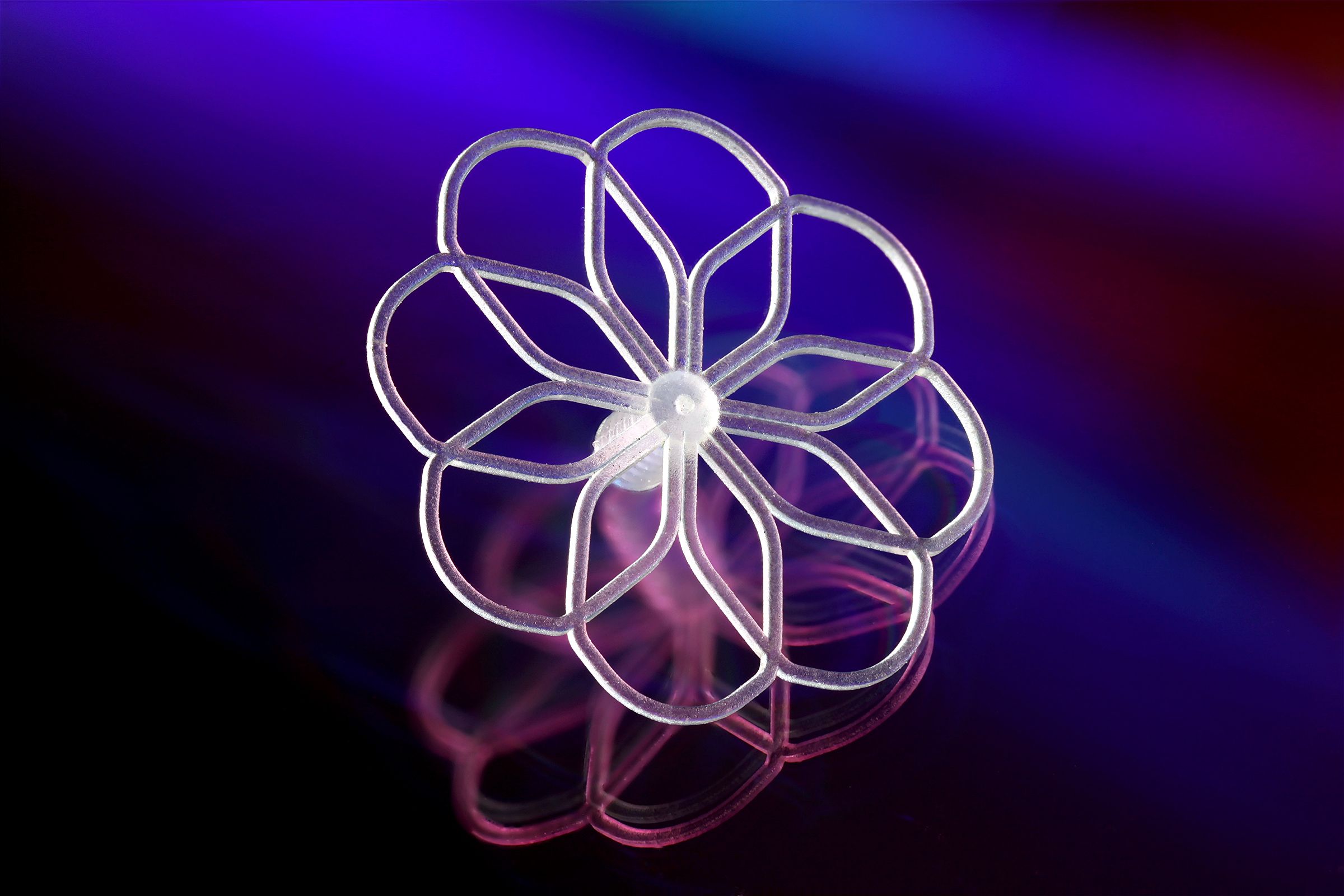
This catheter tip ablation head features a 0.009″ (0.23 mm) wide webbing. The challenging design features long, looping channels that create multiple intersecting flow paths. Preventing one or more of these channels from prematurely solidifying and causing a “short-shot” is only possible with the right micromolding equipment.
2. What are the most challenging materials for thin-wall molding?
Material | Thinnest wall possible* |
1. Elastomers | .010” |
2. Polycarbonate | .007” |
3. Polyurethane | .005” |
4. PEEK | .005” |
*Achievable thinnest wall value highly dependent on geometry and aspect ratio.
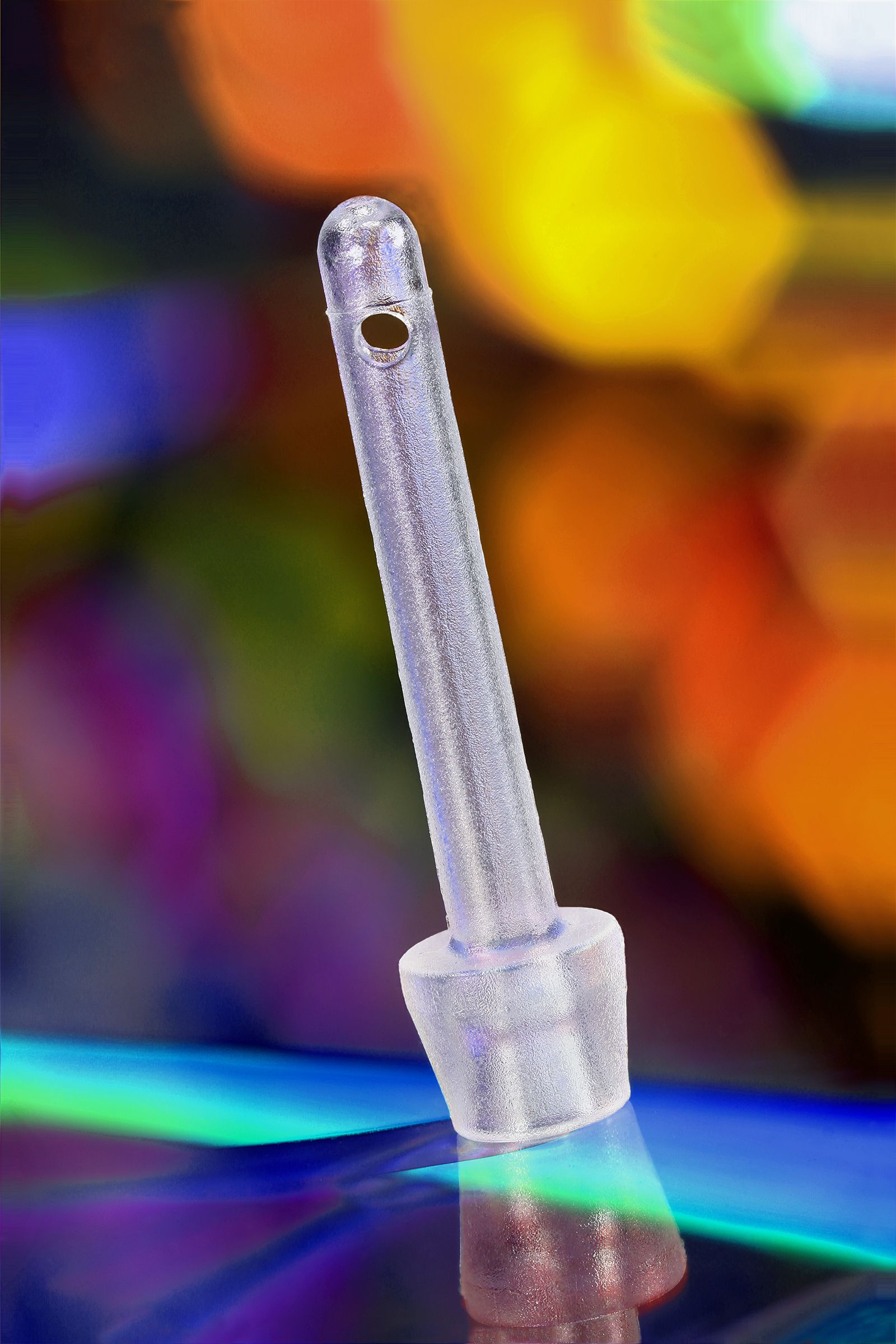
This thin-wall flow tube device made from PC (Polycarbonate) features a .0065″ outer diameter and .0046″ inner diameter, with a .033″ diameter hole. The device is about 0.6″ long.
3. How does this relate to overmolding? Do the same rules apply with these materials and overmolding? Or can it be more challenging? If so, why?
For higher-heat materials, the challenge with overmolding lies in keeping inserts that are placed in and out of the mold at a mold temperature to allow the material to consistently cooperate. This prompts the need to use tools to keep inserts at mold temperature when they are outside of the mold. This step is crucial to ensure proper adhesion of the plastic to substrate and combat flow issues.
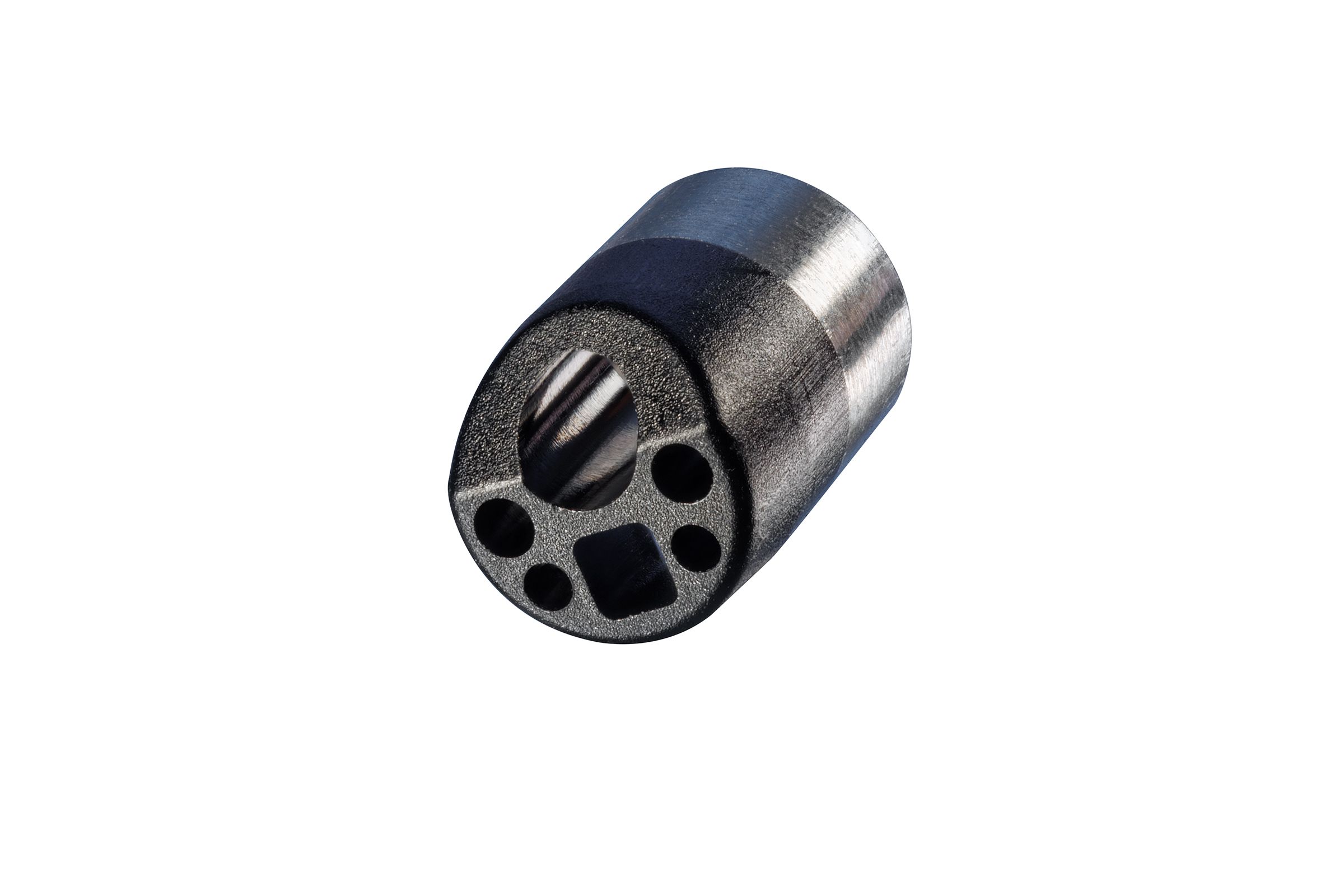
The catheter tip is comprised of a stainless steel insert overmolded with Ultem. This surgical device boasts extremely thin walls measuring .005″ wall thickness at the overmolded section of the metal ring. The design also features +/- .001″ tolerances throughout.
4. What is the key to successful and consistent thin-wall micromolding?
It is a combination of material science and an exact tool, and it all starts with the tool. Exactness of the tool is step one and then it comes down to how the material is processed while keeping its relationship with the tool in mind. When it comes to molding thin walls, mold temperature is an extremely important parameter (i.e. how the mold is cooled and heated). Overall, building the tool to the highest standard and applying molding parameters that optimally interact with the viscosity of the material is imperative for filling the thinnest walls.
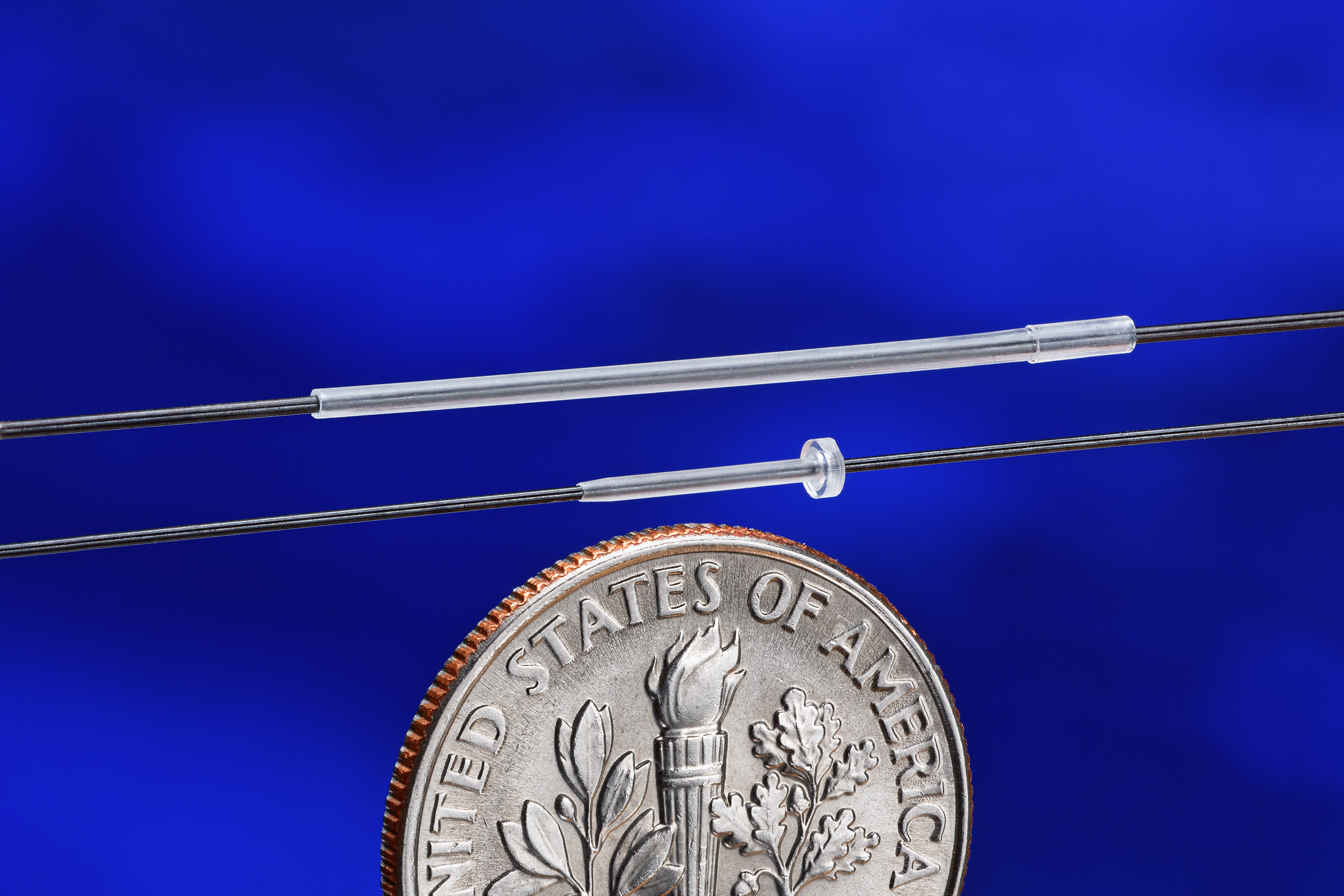
Yes, long-distance ultra-thin walls are possible with micro injection molding—but only with highly capable tooling and molding equipment and techniques. The Polypropylene drug delivery straw (top) features a .005″ long-distance thin wall. The thin-walled micromolded cannula (bottom) design includes walls as thin as .0025″.
5. Anything else about thin-wall molding that makes MTD a specialist in this department?
Equipment plays an important role in advanced molding of ultra-thin-wall medical components. MTD’s molding presses are highly tuned for applications like this to ensure shot-to-shot consistency or process repeatability. It comes down to high caliber equipment and skilled personnel that reach out beyond the basics—many internal R&D studies and years of thin-wall molding expertise allowed us to create a database for tackling ultra-thin wall projects with various materials.